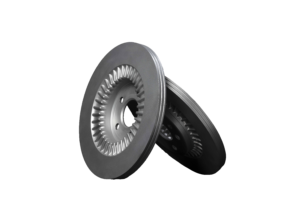
The SiCAlight brake disc from AC Floby offers a durable solution that reduces corrosion and particle emissions. As the automotive industry moves inexorably towards electrification, manufacturers are looking to make lightweighting gains wherever they can find them.
Much of this effort is focused on aluminium, which is lighter and less corrosive than other materials. In terms of components, aluminium has been used sparingly in the past – mainly in niche applications – but there is increasing interest in developing more aluminium parts for electric and plug-in hybrid vehicles as automakers try to keep weight to a minimum.
Brake discs have typically been made of cast iron, but aluminium MMC (Metal Matrix Composite) offers many benefits – not least the reduction of particle emissions and the improved durability of components that have traditionally required regular replacement.
AC Floby has been investing substantial time and resources to develop our aluminium brake discs to be more durable and environmentally sustainable. Uniquely, our aluminium brake discs, SiCAlight, is an optimised combination of silicon carbides and aluminium, creating a safe and lightweight braking system that reduces energy consumption and increases range at the same time.
Corrosion and emissions
In the past, the main challenge for the brake disc industry has been in maintaining performance while reducing wear. But electrification causes different problems. Drivers in electric vehicles use their brakes a lot less frequently, and there is a misconception that this is a positive thing. But while it certainly means brake discs will not wear out as quickly, they are still subject to the elements, and therefore still susceptible to corrosion.
Traditional cast iron brake discs corrode faster when they are not being used, and the journey from cosmetic corrosion to catastrophic loss of primary function is a big headache for manufacturers.
Automakers are now looking at different ways of solving the problem of corrosion in electric vehicles. Durable and maintenance free components are becoming more important – and, despite its higher component cost, aluminium presents an attractive option due to its lighter weight and resistance to wear and corrosion. Without the need for regular replacement, aluminium discs actually represent the most cost-effective option over the lifetime of the vehicle.
Another big problem with braking is the contribution it makes to the creation of particle emissions.
The automotive industry has successfully managed to reduce exhaust emissions steadily – indeed they have halved since the turn of the century – but non-exhaust emissions remain a huge issue. They have remained stubbornly flat in the last two decades, and, since 2011, have actually overtaken exhaust emissions in terms of the number of particles they are producing per vehicle.
These emissions are made up of a variety of causes, including tyre wear and the resuspension of particles on the road. But around a third of non-exhaust emissions are caused by the braking process. Not only that, braking produces bigger particles that are more metallic and toxic than any other emissions. Studies have shown the effect this is having on air quality and how harmful it can be to humans. Even electric vehicles in urban areas will produce a significant amount of non-exhaust emissions.
With exhaust emissions, it was much easier to mitigate and legislate. Manufacturers were incentivised to develop new technologies, there were big public awareness programmes and the move towards electrification meant positive results were almost inevitable. But it has proved to be much harder to reduce non-exhaust emissions in the same way.
The future of brake discs
Keeping these challenges in mind, AC Floby considered several factors when developing our brake discs.
We knew that SiCAlight would have to be:
1. Lightweight
An aluminium-based material results in a 30-70% lighter brake disc than the cast iron equivalent. It also makes the components easy to recycle, reduces fuel consumption and particle emissions.
2. Corrosion resistant
Rust is a big problem, with even minor corrosion decreasing the brake force of a disc. So, SiCAlight needed to be rust-proof to ensure long-lasting results.
3. Durable
Aluminium MMC brake discs have four times the durability of an average cast iron equivalent meaning they should never have to be replaced during a car’s entire lifespan. They should also be able to operate in harsh environments – and be fully recyclable.
4. Able to reduce particle emissions
The SiCAlight brake disc needed to be environmentally sound and drastically reduce the amount of particles emitted when braking.
SiCAlight – several years in the making
While aluminium brake discs are not unique to AC Floby, our expertise and attention to detail have become our trademark. We have used years of experience to create an optimised, homogenous process that is all our own. Our method involves adding 20% volume of silicon carbides into the aluminium melt – which is then evenly distributed in our unique mixing process. Everything from the squeeze casting to the surface texturing is fulfilled in-house.
It hasn’t been an easy road, and it has involved years of refinement and technical development. But the alternative – which is to buy pre-mixed components that then have to be re-melted – can contribute to a significant loss of quality. Although we are a reasonably small operation that is not typically suited to high volume production, we feel strongly that the extra effort has given us an optimised product.
AC Floby has always worked towards these principles. Our experience in automotive components dates back to the 1950s, and SiCAlight has actually been 25 years in the making, with the first prototypes developed in 1995. Much of that time has been spent in rigorous testing and dimensioning work. SiCAlight discs are subjected to multiple tests under different braking scenarios:
Alpine descent – Features continuous braking over a sustained period of time on steep slopes – constant energy input on the brakes for long periods (up to 20 minutes)
Fading – The regular switch from hard acceleration to hard braking, either in and out of traffic, or on the motorway – requiring transient energy input over a short period of time
Single-stop – Often an emergency brake right down to 0kph, the ‘panic stop’ causes the toughest mechanical stresses on the brake discs – transient energy input in a very short period of time (<10 secs)
All of these tests are designed to add to the durability of the discs and have resulted in continuous improvement.
Results and comparison with cast iron discs
The most obvious immediate advantage in the aluminium/silicon carbides product is weight reduction. At just 6.7kg, the SiCAlight is typically around half the weight of the cast iron disc, with a saving of 30%-70% unsprung mass depending on integration and requirements.
The other huge advantage is that the brake discs will now last the lifetime of the car. The silicon carbides in the mix make them entirely resistant to wear and corrosion. Our testing shows that you can drive for 100,000 km with SiCAlight brake discs, and they remain dimensionally the same as if they were new.
While high-performance vehicles may stay with high-performance brake systems, the SiCAlight product is perfect for mass-production vehicles – especially where manufacturers are looking for lightweighting solutions. With the electric and hybrid markets now beginning to dominate, the future is about developing an automotive ecosystem of sustainable production and environmental integrity.
About SiCAlight
SiCAlight is an aluminium alloy disc reinforced with 20% Silicon Carbide (SiC) particles.
The patented technology of etching the brake disc surface enables the rapid development of a friction film and creates the right level of friction between pad and disc using a cost-effective manufacturing process.
• Weight reduction about 30 % – 70 % vs. cast iron disc
• Low particle emission
• No rust/corrosion
• Reduced cost of ownership
About AC Floby
Automotive Components Floby (AC Floby) was founded in 1957 and delivers parts such as brake discs, wheel hubs and connecting rods to automotive companies all over the world.
Driven by key values of knowledge and tradition, all the company’s products are manufactured according to the industry’s highest standards in quality, precision and environmental impact. To further optimize the process for each product, AC Floby technicians work closely with customers to provide expert support and smooth workflow.
Through strong collaboration with national and international universities and key customers, AC Floby fosters product development. With its know-how in aluminium parts production and machining, the company is at the forefront of lightweight components technology.
Read more about the brake disc at www.sicalight.com
By Adam Thomas, Development Engineer at AC Floby